Hybrid vehicle drivetrain
Petroleum electric hybrid vehicles make use of both an on-board rechargeable energy storage system (RESS) and a fueled power source for vehicle propulsion. There are many ways to accomplish this.
Types by drivetrain structure
Parallel hybrid
Parallel hybrid systems, which are most commonly produced at present, have both an internal combustion engine (ICE) and an electric motor connected to a mechanical transmission. Most designs combine a large electrical generator and a motor into one unit, often located between the combustion engine and the transmission, replacing both the conventional starter motor and the alternator. To store power, a hybrid uses a large battery pack with a higher voltage than the normal automotive 12 volts. Accessories such as power steering and air conditioning are powered by electric motors instead of being attached to the combustion engine. This allows efficiency gains as the accessories can run at a constant speed, regardless of how fast the combustion engine is running.
Parallel hybrids can be categorized by the way the two sources of power are mechanically coupled. If they are joined at some axis truly in parallel, the speeds at this axis must be identical and the supplied torques add together. Most electric bicycles are in effect of this type. When only one of the two sources is being used, the other must either also rotate in an idling manner or be connected by a one-way clutch or freewheel. With cars it is more usual to join the two sources through a differential gear. Thus the torques supplied must be the same and the speeds add up, the exact ratio depending on the differential characteristics. When only one of the two sources is being used, the other must still supply a large part of the torque or be fitted with a reverse one-way clutch or automatic clamp.
Parallel hybrids can be further categorized depending upon how balanced the different portions are at providing motive power. In some cases, the combustion engine is the dominant portion; the electric motor turns on only when a boost is needed. Others can run with just the electric system operating.
Series hybrid
In a series hybrid system, the combustion engine drives an electric generator instead of directly driving the wheels. The generator both charges a battery and powers an electric motor that moves the vehicle. When large amounts of power are required, the motor draws electricity from both the batteries and the generator. A complex transmission is not needed, as electric motors are efficient over a wide speed range. Some vehicle designs have separate electric motors for each wheel. Series hybrids can be also be fitted with a supercapacitor or a flywheel, which can improve efficiency by minimizing the losses in the battery.
The advantage of a series hybrid is the lack of a mechanical link between the combustion engine and the wheels. The combustion engine runs at a constant and efficient rate, even as the car changes speed. During stop-and-go city driving, series hybrids are relatively the most efficient.
A weakness is that the power from the combustion engine has to run through both the generator and electric motor. During long-distance highway driving, the electrical transmission can be less efficient than a conventional transmission.
The use of one motor per wheel eliminates the conventional mechanical transmission elements (gearbox, transmission shafts, differential). If the motors are integrated into the wheels, the unsprung mass increases, decreasing ride performance. If the motors are attached to the vehicle body, flexible couplings are required. Advantages of individual wheel motors include simplified traction control and all wheel drive, and allowing lower floors, which is useful for buses. Some 8x8 all-wheel drive military vehicles use individual wheel motors.
Combined hybrid
Combined hybrid systems have features of both series and parallel hybrids. They incorporate power-split devices allowing for power paths from the engine to the wheels that can be either mechanical or electrical. The main principle behind this system is the decoupling of the power supplied by the engine (or other primary source) from the power demanded by the driver.
In a conventional vehicle, a larger engine is used to provide acceleration from standstill than one needed for steady speed cruising. This is because a combustion engine's torque is minimal at lower RPMs, as the engine is its own air pump. On the other hand, an electric motor exhibits maximum torque at stall and is well suited to complement the engine's torque deficiency at low RPMs. In a combined hybrid, a smaller, less flexible, and highly efficient engine can be used. It is often a variation of the conventional Otto cycle, such as the Miller or Atkinson cycle. This contributes significantly to the higher overall efficiency of the vehicle, with regenerative braking playing a much smaller role.
Interesting variations of that simple theme, as very well known (implemented in the Toyota Prius) are the
- addition of a fixed gear second planetary gearset as used in the Lexus RX400h and Toyota Highlander Hybrid. This allows for a motor with less torque but higher power (and higher maximum rotary speed), ie. higher power density
- addition of a ravigneux-type planetary gear (planetary gear with 4 shafts instead of 3) and two clutches as used in the Lexus GS450h. By switching the clutches, the gear ratio from MG2 (the "drive" motor) to the wheel shaft is switched, either for higher torque or higher speed (up to 250 km/h / 155 mph) while sustaining better transmission efficiency.
The Toyota Hybrid System THS / Hybrid Synergy Drive mode of operation with only a single power split device (incorporated as a single 3 shaft planetary gearset) is a typical example which can also be called Input-Split Hybrid, due to the fact that a fixed amount of torque is transferred via the electrical path from the engine to the wheels. This in turn makes this setup very simple in mechanical terms, but does have some drawbacks of its own. For example the maximum speed is mainly limited by the speed of the smaller electric motor. Also, the efficiency of the transmission is heavily dependent on the amount of power being transmitted over the electrical path, as multiple conversions, each with their own, less than perfect efficiency, lead to a low efficiency of that path (~0.7) compared with the purely mechanical path (~0.98). Especially in higher speed regimes (>120 km/h or 70 mph) the efficiency (of the transmission alone) therefore drops below that of a generic automatic transmission with hydrodynamic coupler.
General Motors, BMW, and DaimlerChrysler are working together on a so-called Two-Mode Hybrid system which is a full hybrid plus additional efficiency improvements as part of the Global Hybrid Cooperation. The technology will be released in fall of 2007 on the Chevrolet Tahoe Hybrid. The system was also featured on the GMC Graphite SUV concept vehicle at the 2005 North American International Auto Show in Detroit.
The main difference to the Input-Split Hybrid is the addition of a second planetary gearset, and the addition of four clutches (which can actually operate as one). This enables the switching (two-modes) of the percentage of mechanically vs. electrically transmitted power, in order to cope both with low-and high-speed regimes, enabling smaller motors to do the job of larger motors when compared to a single mode type system. The four fixed gears enable the Two-mode hybrid to function like a conventional parallel hybrid under high continuous power regions, like sustained high speed cruising or during towing. Full electric boost is available in fixed gear modes.
Types by degree of hybridization
Full hybrid
A full hybrid, sometimes also called a strong hybrid, is a vehicle that can run on just the engine, just the batteries, or a combination of both. The Prius and Escape Hybrids are examples of this, as both cars can be moved forward on battery power alone. A large, high-capacity battery pack is needed for battery-only operation. These vehicles have a split power path that allows more flexibility in the drivetrain by interconverting mechanical and electrical power, at some cost in complexity. To balance the forces from each portion, the vehicles use a differential-style linkage between the engine and motor connected to the head end of the transmission.
The Toyota brand name for this technology is Hybrid Synergy Drive, which is being used in the Prius, Highlander sport-utility vehicle (SUV), and Camry. A computer oversees operation of the entire system, determining which half should be running, or if both should be in use, shutting off the internal combustion engine when the electric motor is sufficient to provide the power. The operation of the Prius can be divided into five (5) distinct regimes:
- Electric vehicle mode
- Cruise mode
- Battery charge mode
- Power boost mode
- Negative split mode
In (1), the engine is off, and the battery provides electrical energy to power the motor (or the reverse when regenerative breaking is engaged). Used for idling as well when the battery state-of-charge [SOC] is high. In (2), the vehicle is cruising (i.e. not accelerating), and the engine can meet the road load demand. The power from the engine is split between the mechanical path and the generator. The latter provides electrical energy to power the motor, whose power is summed mechanically with the engine. If the battery SOC is low, part of the power from the generator is directed towards charging the battery. Regime (3) is used for idling as well, except that in this case the battery SOC is low and requires charging, which is provided by the engine and generator. Regime (4) consists of situations where the engine cannot meet the road load demand, and the battery is then used to power the motor to provide a boost to the engine power. Finally, in (5) the vehicle is cruising and the battery SOC is high. The battery provides power to both the motor (to provide mechanical power) and to the generator. The generator converts this to mechanical energy that it directs towards the engine shaft, slowing it down (although not altering its torque output). The purpose of this engine "lugging" is to increase the fuel economy of the vehicle.
The hybrid drivetrain of the Prius, in combination with aerodynamics and optimizations in the engine itself to reduce drag, results in 80%–100% gains in fuel economy compared to four-door conventional cars of similar weight and size.
Power assist hybrid

Power assist hybrids use the engine for primary power, with a torque-boosting electric motor also connected to a largely conventional powertrain. The electric motor, mounted between the engine and transmission, is essentially a very large starter motor, which operates not only when the engine needs to be turned over, but also when the driver "steps on the gas" and requires extra power. The electric motor may also be used to re-start the combustion engine, deriving the same benefits from shutting down the main engine at idle, while the enhanced battery system is used to power accessories.
Honda's hybrids including the Insight use this design, leveraging their reputation for design of small, efficient gasoline engines; their system is dubbed Integrated Motor Assist (IMA). Assist hybrids differ fundamentally from full hybrids in that they cannot run on electric power alone. However, since the amount of electrical power needed is much smaller, the size of the battery systems is reduced. Starting with the 2006 Civic Hybrid, the IMA system now can propel the vehicle solely on electric power during medium speed cruising.
A variation on this type of hybrid is the Saturn VUE Green Line hybrid system that uses a smaller electric motor (mounted to the side of the engine), and battery pack than the Honda IMA, but functions similarly.
Another variation on this type is Mazda's e-4WD system, offered on the Mazda Demio sold in Japan. This front-wheel drive vehicle has an electric motor which can drive the rear wheels when extra traction is needed. The system is entirely disengaged in all other driving conditions, so it does not enhance performance or economy.
Ford has dubbed Honda's hybrids "mild" in their advertising for the Escape Hybrid, arguing that the Escape's full hybrid design is more efficient. However, assist hybrids should not be confused with actual mild hybrids like the Chevrolet Silverado Hybrid. The term mild hybrid is not standardized, and its use is often more inspired by marketing than by technical considerations.
Mild hybrid

Mild hybrids are essentially conventional vehicles with oversized starter motors, allowing the engine to be turned off whenever the car is coasting, braking, or stopped, yet restart quickly and cleanly. Accessories can continue to run on electrical power while the engine is off, and as in other hybrid designs, the motor is used for regenerative braking to recapture energy. The larger motor is used to spin up the engine to operating rpm speeds before injecting any fuel.
Many people do not consider these to be hybrids at all, and these vehicles do not achieve the fuel economy of full hybrid models. A major example is the 2005 Chevrolet Silverado Hybrid, a full-size pickup truck. Chevrolet was able to get a 10% improvement on the Silverado's fuel efficiency by shutting down and restarting the engine on demand. Mild hybrids often use 42 volt systems to supply the power needed for the startup motor, as well as to compensate for the increasing number of electronic accessories on modern vehicles.
General Motors followed the pickup truck hybrid with their Belt alternator starter (BAS) hybrid system, used in the 2007 Saturn VUE Green Line. For its "start-stop" functionality, it operates similarly to the system in the Silverado. But the GM BAS has broader hybrid functionality as the electric motor can also provide modest assist under acceleration and during steady driving, and captures regenerative braking, resulting in a 20% improvement in fuel efficiency; thus, the BAS can also be considered an Assist hybrid.
Plug-in hybrid
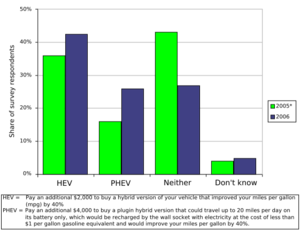
Template:Main A plug-in hybrid electric vehicle (PHEV) is a full hybrid, able to run in electric-only mode, with larger batteries and the ability to recharge from the electric power grid. They are also called gas-optional, or griddable hybrids. Their main benefit is that they can be gasoline-independent for daily commuting, but also have the extended range of a hybrid for long trips. They can also be multi-fuel, with the electric power supplemented by diesel, biodiesel, or hydrogen. The Electric Power Research Institute's research indicates a lower total cost of ownership for PHEVs due to reduced service costs and gradually improving batteries. The "well-to-wheel" efficiency and emissions of PHEVs compared to gasoline hybrids depends on the energy sources of the grid (the US grid is 50% coal; California's grid is primarily natural gas, hydroelectric power, and wind power). Particular interest in PHEVs is in California where a "million solar homes" initiative is under way, and global warming legislation has been enacted.
Prototypes of PHEVs, with larger battery packs that can be recharged from the power grid, have been built in the U.S., notably at Prof. Andy Frank's Hybrid Center at UC Davis and one production PHEV, the Renault Kangoo, went on sale in France in 2003. DaimlerChrysler is currently building PHEVs based on the Mercedes-Benz Sprinter van. Light Trucks are also offered by Micro-Vett SPA the so called Daily Bimodale.
The California Cars Initiative has converted the '04 and newer Toyota Prius to become a prototype of what it calls the PRIUS+. With the addition of 300 lb of lead-acid batteries, the PRIUS+ achieves roughly double the gasoline mileage of a standard Prius and can make trips of up to 10 miles using only electric power. Plug -in Hybrid are like Series Hybrids.
Some scientists believe that PHEVs will soon become standard[1] in the automobile industry.
See also: vehicle to grid
Types by nature of the power source
Electric-internal combustion engine hybrid
There are many ways to create an electric-internal combustion hybrid. The variety of electric-ICE designs can be differentiated by how the electric and combustion portions of the powertrain connect, at what times each portion is in operation, and what percent of the power is provided by each hybrid component. Two major categories are series hybrids and parallel hybrids, though parallel designs are most common today.
Most hybrids, no matter the specific type, use regenerative braking to recover energy when slowing down the vehicle. This simply involves driving a motor so it acts as a generator.
Many designs also shut off the internal combustion engine when it is not needed in order to save energy. That concept is not unique to hybrids; Subaru pioneered this feature in the early 1980s, and the Volkswagen Lupo 3L is one example of a conventional vehicle that shuts off its engine when at a stop. Some provision must be made, however, for accessories such as air conditioning which are normally driven by the engine. Furthermore, the lubrication systems of internal combustion engines are inherently least effective immediately after the engine starts; since it is upon startup that the majority of engine wear occurs, the frequent starting and stopping of such systems reduce the lifespan of the engine considerably. Also, start and stop cycles may reduce the engine's ability to operate at its optimum temperature, thus reducing the engine's efficiency.
Fuel cell hybrid
Fuel cell vehicles are often fitted with a battery or supercapacitor to deliver peak acceleration power and to reduce the size and power constraints on the fuel cell (and thus its cost); this is effectively also a series hybrid configuration.
Hydraulic hybrid
A hydraulic hybrid vehicle uses hydraulic and mechanical components instead of electrical ones. A variable displacement pump replaces the motor/generator, and a hydraulic accumulator (which stores energy as highly compressed nitrogen gas) replaces the batteries. The hydraulic accumulator, which is essentially a pressure tank, is potentially cheaper and more durable than batteries. Hydraulic hybrid technology was originally developed by Volvo Flygmotor and was used experimentally in buses from the early 1980s and is still an active area.
Initial concept involved a giant flywheel (see Gyrobus) for storage connected to a hydrostatic transmission, but it was later changed to a simpler system using a hydraulic accumulator connected to a hydraulic pump/motor. It is also being actively developed by Eaton and several other companies, primarily in heavy vehicles like buses, trucks and military vehicles. An example is the Ford F-350 Mighty Tonka concept truck shown in 2002. It features an Eaton system that can accelerate the truck up to highway speeds.
Pneumatic hybrid
Compressed air can also power a hybrid car with a gasoline compressor to provide the power. Moteur Developpement International in France produces such air cars. A team led by Tsu-Chin Tsao, a UCLA mechanical and aerospace engineering professor, is collaborating with engineers from Ford to get Pneumatic hybrid technology up and running. The system is similar to that of a hybrid-electric vehicle in that braking energy is harnessed and stored to assist the engine as needed during acceleration.
Human power and environmental power hybrids
Many land and water vehicles use human power combined with a further power source. Common are parallel hybrids, e.g. a boat being rowed and also having a sail set, or motorized bicycles. Also some series hybrids exist, see in hybrid vehicle. Such vehicles can be tribrid vehicles, combining at the same time three power sources e.g. from on-board solar cells, from grid-charged batteries, and from pedals.
Hybrid vehicle operation modes
Hybrid vehicles can be used in different modes. The figure shows some typical modes for a parallel hybrid configuration.
Adding powertrains and aftermarket kits
One can install conmarket or aftermarket powertrain to a vehicle to hybridise it.
The conmarket solution is used when the user buys the glider and the hybrid (two engines) or all-electric (only an electric motor) powertrain kit to the automaker and receives it installed in the car. Also an (electric or hybrid) powertrain can be added to a glider by a third party aftermarket installer (see plug-in hybrid).
External links
- ↑ "Hybrid Vehicles Gain Traction", Scientific American, January 13,2006